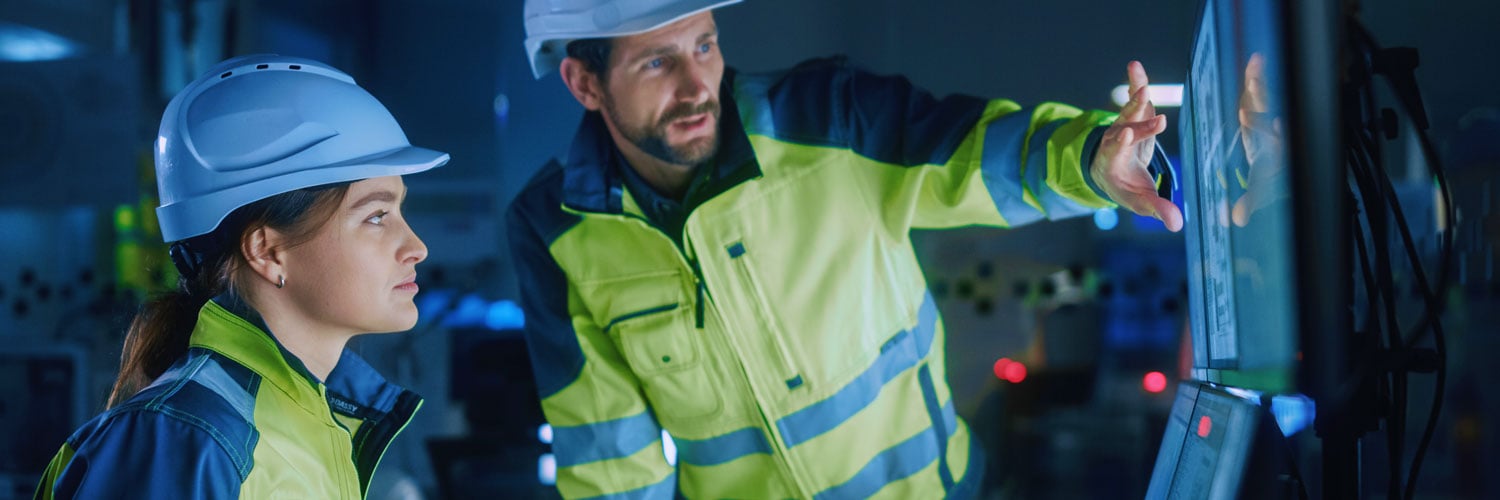
When your computerized maintenance management system (CMMS) already has a calibration module, why would you buy dedicated calibration software?
It’s a fair question and one that we frequently get asked! The reasons can vary, depending on the application. Are you maybe comparing apples to oranges?
There are different kinds of dedicated calibration software products out there, each with somewhat different functionalities. Although they have the same name, they are all different in one way or another.
Does integrating dedicated calibration software with your CMMS bring you the best of both worlds, or just a big mess?
In this article we look at the various setups and compare these different scenarios.
If this sounds interesting, please keep on reading.
Table of contents
- CMMS and calibration
- The problem with pen and paper
- CMMS vs. dedicated calibration management software
- Calibration software - manual or automatic?
- Integration – the best of both worlds!
- Beamex calibration ecosystem
- Related blog posts
CMMS and calibration
CMMS, asset management systems, and enterprise resource planning (ERP) systems include a variety of different functionalities and are implemented for a certain purpose. They are not designed specifically for calibration management. Although they have some calibration functionality, this can be quite limited.
Sure, there can be an add-on calibration module with basic functionality for calibration management, but these kinds of systems do not have the same level of sophistication as dedicated calibration software designed specifically for the purpose of calibration.
Sometimes these add-ons still require manual data entry methods such as a pen and paper to document calibrations! C’mon, this is the 21st century!
The problem with pen and paper
With digitalization becoming the norm in industry, you could be forgiven for thinking that calibration is already taken care of by the calibration module of your CMMS. But, as mentioned above, calibration results may still need to be documented manually using pen and paper. The papers are then archived, or the calibration data is subjected to another error-prone manual step – entering it into the calibration module using a computer keyboard.
In the worst-case scenario the calibration data is not stored digitally in the CMMS at all and may simply be scanned. This brings further limitations as you can’t analyze any data from a scanned document.
This is also the case if the data is stored in a paper archive. For example, you can’t easily check the detailed results of the previous calibrations performed. Also, it’s very difficult to find data for regulatory audits. This process also brings with it all the data quality and integrity issues related to manual data entry. The errors within manually completed files don’t disappear if you scan them or manually transcribe the results from the paper to the CMMS, which as mentioned above, can introduce further errors.
Learn more about the consequences of manual data entry is this blog: Manual Data Entry Errors
Also, we need to consider reverse traceability. This means that if a reference standard (calibrator) is found to be out of specifications during a calibration, you need to investigate where that reference standard has been used. It may have been used for tens or even hundreds of calibrations, and as a result these may all be considered suspect. If all your calibration certificates are in paper format or scanned, it is extremely laborious and time-consuming to go through them to perform reverse traceability. Advanced calibration software would allow you to generate a reverse traceability report at the touch of a button.
Beyond data analysis – or the lack of it if you’re using paper files or scanned documents – there are other, often overlooked, ways in which dedicated calibration management software can help your business shine.
- Sustainability – You might have invested significant time and money in initiatives to create more sustainable working practices, but have you thought about how calibration can make your business more sustainable? A robust calibration process using dedicated software improves efficiency, eliminates paper, and can even extend the lifespan of your equipment.
- Employee wellbeing – Making calibration tasks simpler and less stressful for your technicians can make a huge difference to their wellbeing and can even mark you out as an employer of choice in what is an extremely competitive labor market.
- Product quality – The downstream impact of data integrity or other issues within the calibration processes can compromise the quality of your products. Dedicated calibration software helps to avoid this problem by maintaining data integrity.
- Safety – If you’re making a product that is consumed, for example food or medicine, dedicated calibration management software can give you greater confidence that your product is safe because you can rely on the fact that your in-process measurements are accurate. This is particularly important in cases where a product cannot be destructively tested to confirm it is safe.
CMMS vs. dedicated calibration management software
Let’s take a more detailed look at how the calibration module in a CMMS stacks up against dedicated calibration management software such as Beamex CMX.
- Functionality: Compared to a CMMS module, dedicated calibration management software typically offers more advanced functionality for managing calibration procedures, such as automated calibration scheduling, calibration task management, guided instructions, reference management, calibration uncertainty calculations, reporting, and more.
- Customization: Dedicated calibration management software is typically highly customizable, meaning you can configure it to your specific calibration needs. This can include creating custom calibration procedures, configuring workflows, and integrating the software with other systems. A calibration module in a CMMS typically is more limited in terms of customization options. If you do want to customize your CMMS module with additional calibration functionality, it will be costly to implement and maintain. What’s more, you might not even know what kind of functionality needs to be added. Dedicated software from a reputable provider will take into account the current and future requirements of a large customer base and leverage emerging future technologies, adding new features and functionalities as part of regular updates.
- Integration: While both types of software can integrate with other systems, dedicated calibration management software may offer more seamless integration with other laboratory or process control systems, such as electronic documentation management systems, laboratory information management systems (LIMS), or ERP systems. A CMMS calibration module may only offer limited integration options.
- User interface: Dedicated calibration management software typically offers a user-friendly interface specifically designed for managing calibration processes, which can help to streamline workflows and improve user productivity. A calibration module in a CMMS on the other hand may have a more general user interface that is designed to support a range of maintenance management tasks.
- Cost: Dedicated calibration management software may be more expensive than a calibration module in a CMMS as it offers more advanced functionality and customization options. However, you should find that the additional cost is justified by the improved functionality and productivity gains that dedicated software offers.
Calibration software - manual or automatic?
Not all products that are called calibration management software solutions are the same or offer the same functionalities.
The two main different categories are calibration software where data is entered into the system manually and software that communicates with documenting calibration tools. Let’s look at these two categories in more detail.
1. Calibration software with manual data entry
With these types of systems, you input the data manually with a keyboard. If you don’t carry a laptop with you in the field, then you need to manually document data during the calibration and then input it into the system when you’re back in the office – meaning there are two manual steps in your calibration process!
While this kind of calibration software may offer a lot of functionality once you have the results stored digitally in the system database, including data analysis, the original source data may have gone through multiple manual entry steps before ending up in the system. So, the data may have accidental (or even intentional) errors, and the data quality and integrity could be questionable.
Analyzing non-reliable data is a waste of time and may even be misleading, leading to wrong decisions. “Crap in, crap out”, as they say.
So, in the end using this kind of calibration software is not much better than using a CMMS calibration module.
Learn more about the consequences of manual data entry is this blog: Manual Data Entry Errors
2. Calibration software that communicates with documenting calibrators
With this kind of software there is no need for any manual data entry during the calibration process. Your calibration tools automatically store the calibration data digitally during the calibration. This eliminates the risk of manual error and means that the data cannot be tampered with. The calibrator can even be configured to require an electronic signature from the person who performed the calibration. This is important in highly regulated industries such as the pharmaceutical industry, where data integrity is vital.
Learn more about: Data Integrity in calibration processes, or about Common Data Integrity pitfalls in calibration processes.
A documenting calibrator may even be able to perform the calibration fully automatically, saving time and ensuring a repeatable calibration process every time. Once the calibration is complete and the data is stored in the calibrator, the results can be transferred from the calibrator’s memory to the calibration software, again fully digitally.
Advanced documenting calibrators can also perform an automatic pass or fail decision straight after the calibration. This may sound like a small thing, but what about if you have a square rooting pressure transmitter ranging from -0.1 to 0.6 bar and you get an output of 12.55 mA at 0.1 bar input pressure, while your error limit is 0.5 % of span – does that sound like a pass or fail?
It’s not always easy to calculate in your head – or even with calculator. Sure, if you have a 0 to 100 °C temperature transmitter and the error limit is ± 0.5 °C, it is very easy. A smart documenting calibrator like a Beamex documenting calibrator will automatically tell you if each point is a pass or fail.
Using this kind of calibration management software together with documenting calibrators offers significant advantages over basic calibration software or your CMMS’s calibration module. It will save you a lot of time in calibration, and ensures you have high-quality data available for analysis.
But even with the most advanced calibration software, it’s important to remember that there is still some manual work to do in the process, starting with generating the work order in your CMMS and finally closing it.
But don’t worry, there is a better way to do that too. You can also digitalize and automate this step in the process if you integrate your CMMS and your calibration software. More on that next.
Integration – the best of both worlds!
Creating an end-to-end digital flow of calibration data throughout your business is easily achievable by integrating your CMMS with advanced calibration management software, such a Beamex CMX, that can communicate with documenting calibrators.
Many of our customers have found a better way with this kind of integration.
In practice, in the simplest case this integration works like this: work orders are generated in the CMMS and automatically sent to your calibration management software, and when the calibration is complete in the software, it automatically notifies the CMMS to close the work order.
What our customers say on integration
"With this software integration project, we were able to realize a significant return on investment during the first unit overhaul. It’s unusual, since ROI on software projects is usually nonexistent at first."
Jody Damron, Business Analyst, Salt River Project, US
Read the full Salt River Project case story >>
Beamex calibration ecosystem
Beamex calibration ecosystem is a comprehensive solution for calibration management that includes various hardware and software tools designed to help industries achieve better quality and reliability in their production processes. It consists of three main components: calibration software, calibration equipment, and calibration services.
The calibration software provides a user-friendly interface for managing calibration procedures, storing calibration data, and generating reports. It allows for customizable workflows, automated documentation, and integration with other systems.
The calibration hardware includes portable calibrators, bench calibrators, and pressure controllers that are designed to perform accurate and reliable calibrations in the field or laboratory. These devices are easy to use and feature advanced functions such as automated calibration, data logging, and wireless communication.
Calibration services are also offered by Beamex, which include on-site calibration, instrument maintenance, and training. The services are provided by qualified technicians who are experts in their field and can provide tailored solutions to meet the specific needs of each customer.
Overall, the Beamex calibration ecosystem provides a complete solution for calibration management that can help industries improve their processes, reduce downtime, and comply with regulatory requirements.
Learn more about the Beamex calibration ecosystem on our website >>
Talk with Beamex experts to find the best solution for you >>
Related blog posts
If you liked this post, you might also like these:
- How a business analyst connected calibration and asset management [Case Story]
- CMMS and calibration management integration - Bridging the gap
- Common Data Integrity Pitfalls in Calibration Processes
- Do more with less and generate ROI with an Integrated Calibration Solution
- Manual Data Entry Errors
- Automating the calibration management ecosystem
- Calibration management - transition from paper-based to digital
- The Evolution of Calibration Documentation
Finally, I want to thank my colleague Aidan Farrelly for his great LinkedIn post that sparked the idea for this post. Also, thanks Aidan for your comments while I was writing this.
A Buyer's Guide to Calibration Management Software
If you’re evaluating calibration management software, our Buyer’s Guide to Calibration Managent Software is a must-read. It will give you a clear roadmap to making an informed decision that aligns with your business goals.
Download the Buyer's Guide by clicking the image below:
Discussion