TOPIC
Calibration management
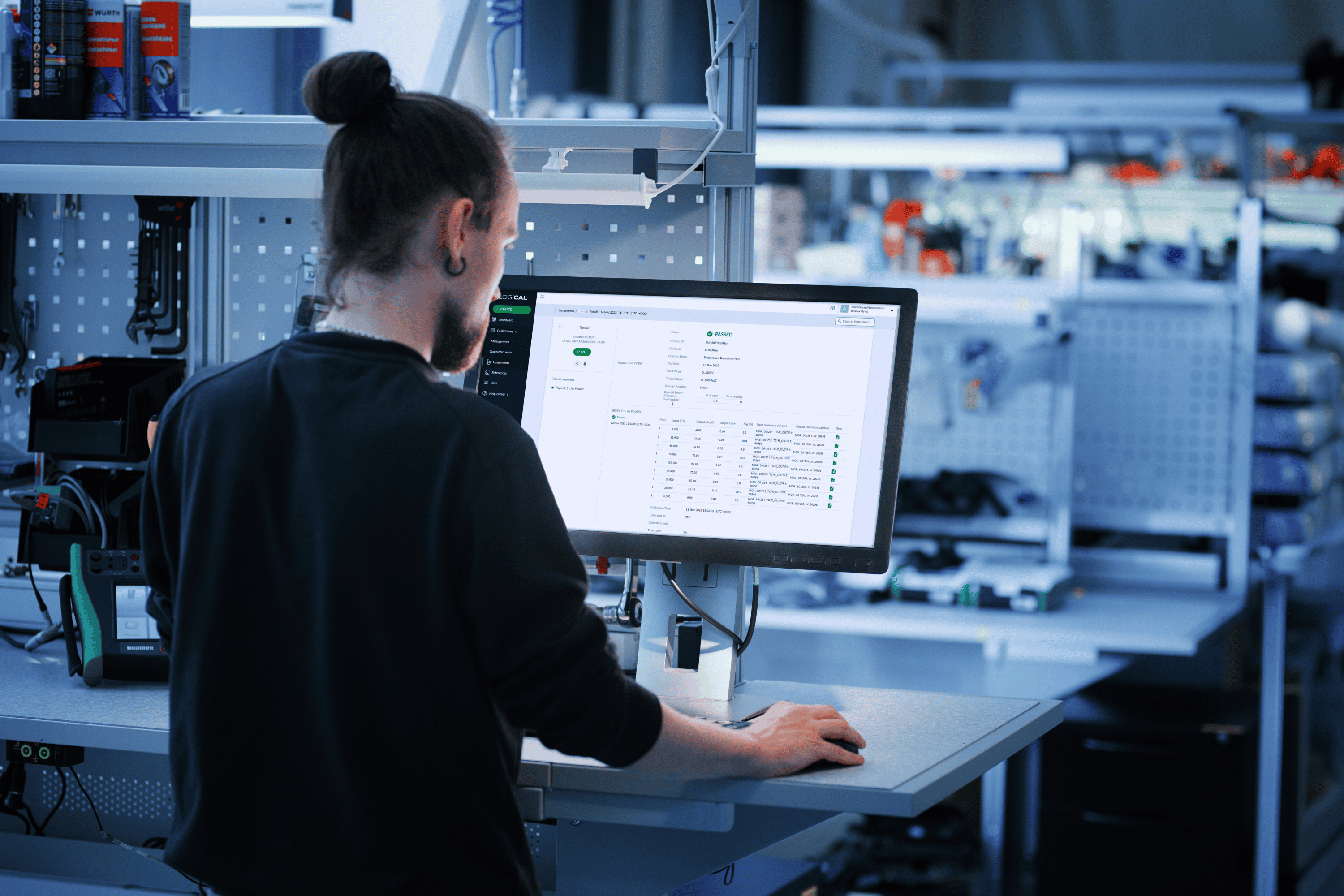
Feb 20, 2025
Cloud vs. On-Premises Calibration Solutions
In the world of calibration management, choosing the right deployment model for your software makes ...
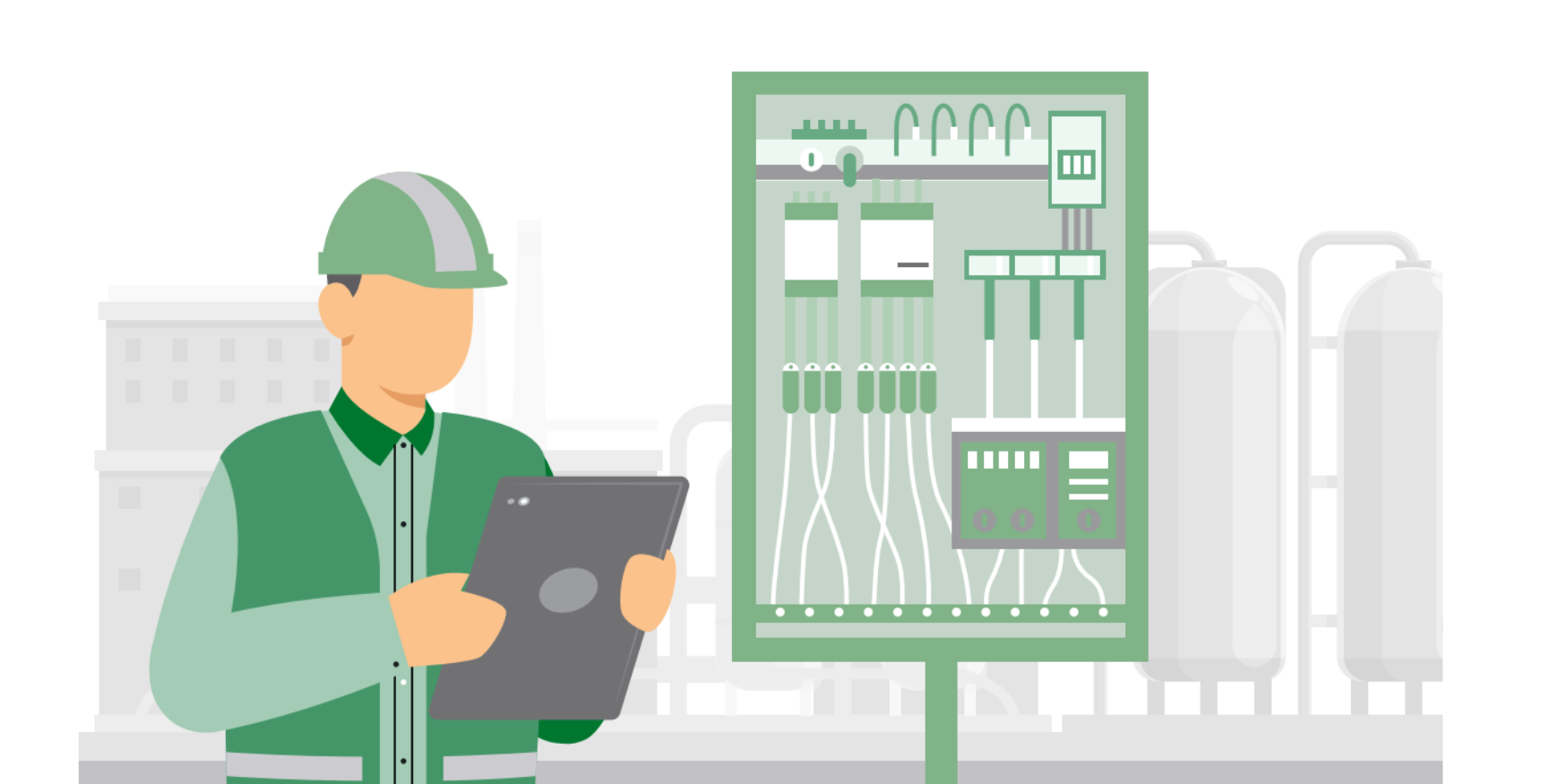
Aug 23, 2024
Calibration Process Savings Calculator [Online calculator]
Are you ready to uncover potential savings within your calibration processes? In this blog, we’re ...
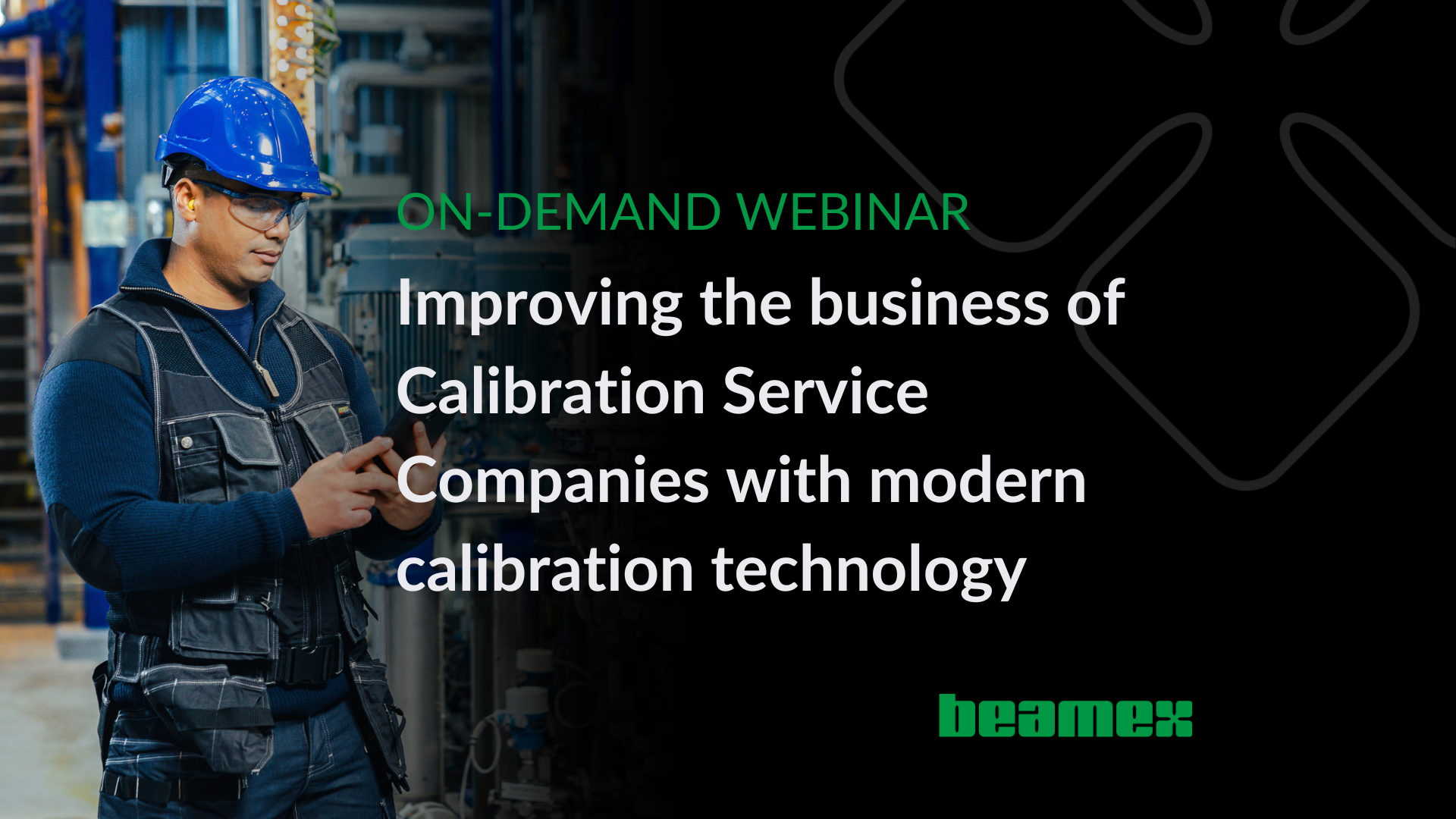
Jul 04, 2024
Revolutionizing calibration services with technology - case story [webinar]
In today's fast-paced world, managing calibration services efficiently is critical. At Douglas ...
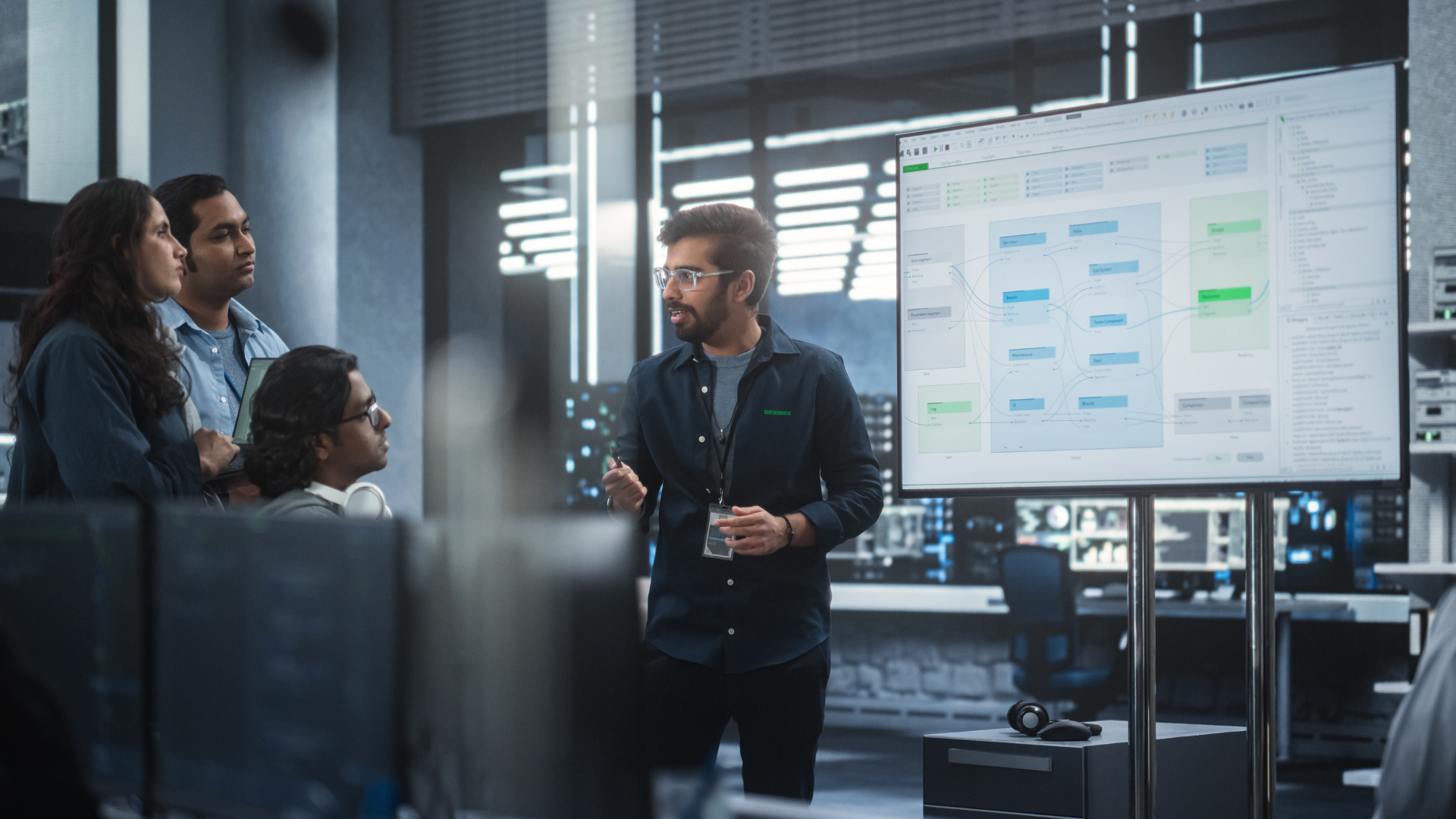
Apr 03, 2024
With empathy to excellence - The secret to great customer service
Empathy is an essential element of great customer service. Along with understanding, it’s the most ...
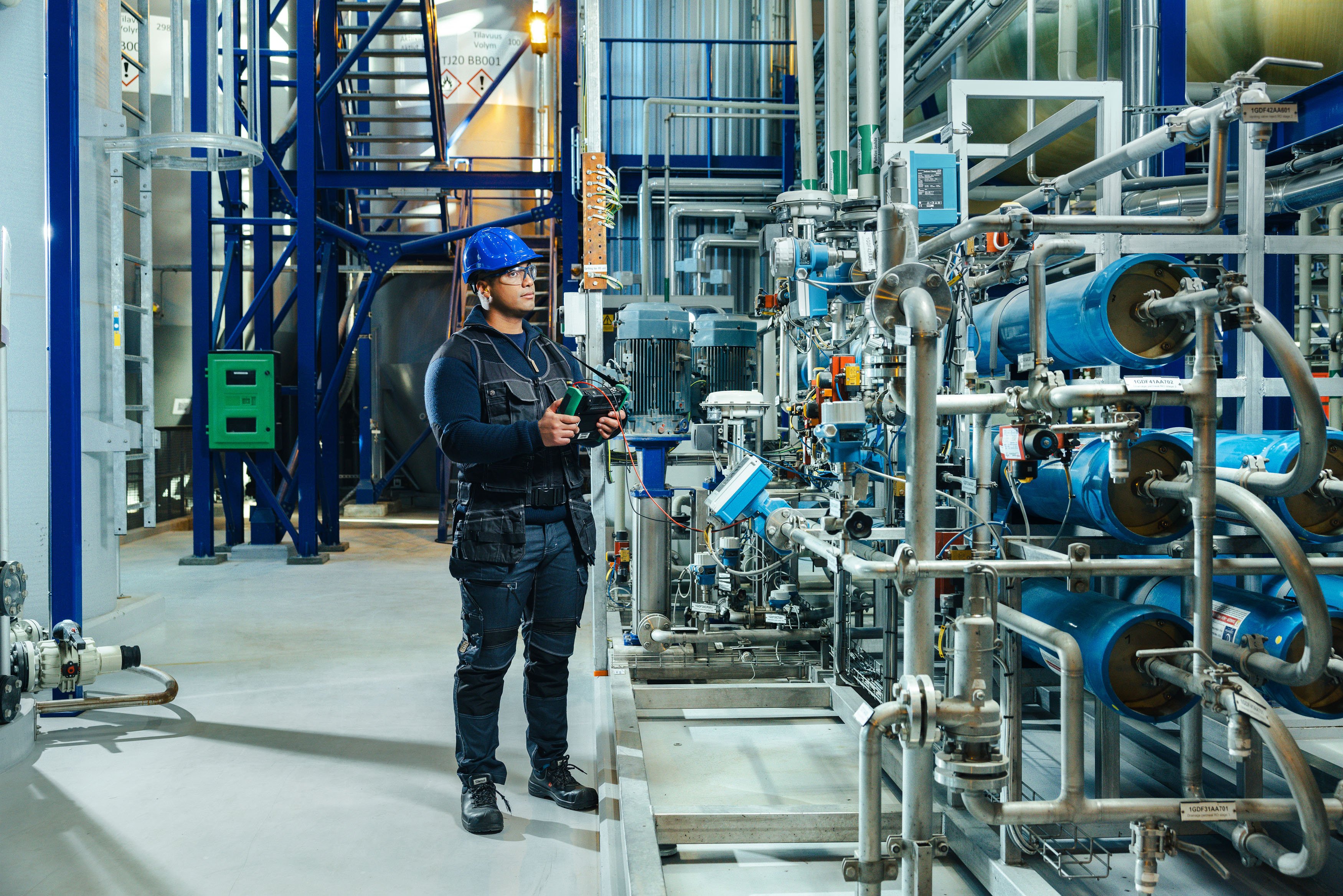
Feb 13, 2024
Calibrating for a Cleaner Future - Unlocking the Potential of Waste to Energy
Waste-to-Energy (WtE) has been around since the first waste incinerator was built in 1874, but the ...
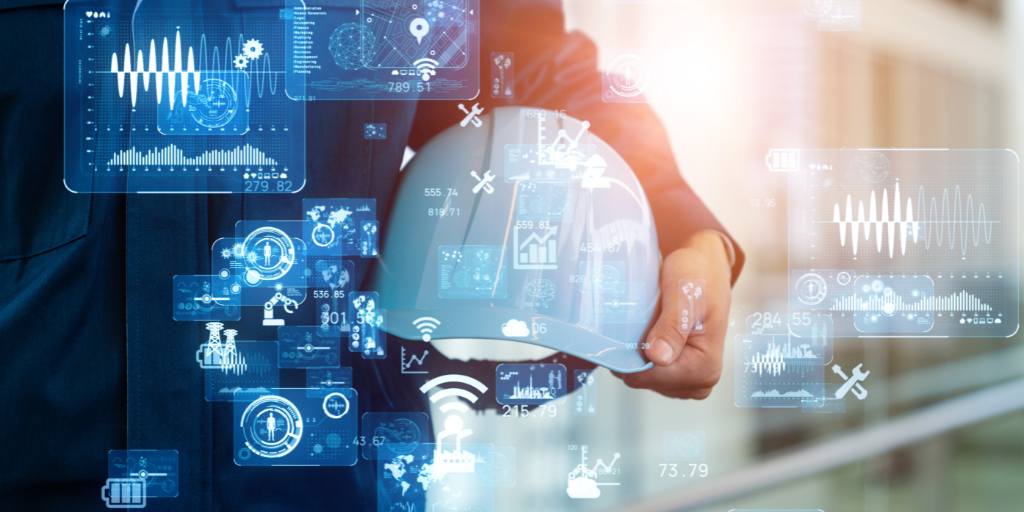
Jan 09, 2024
How an accurate, reliable calibration solution could supercharge your business [Podcast]
Whether you work in manufacturing, pharmaceuticals, healthcare, or any other field that relies on ...
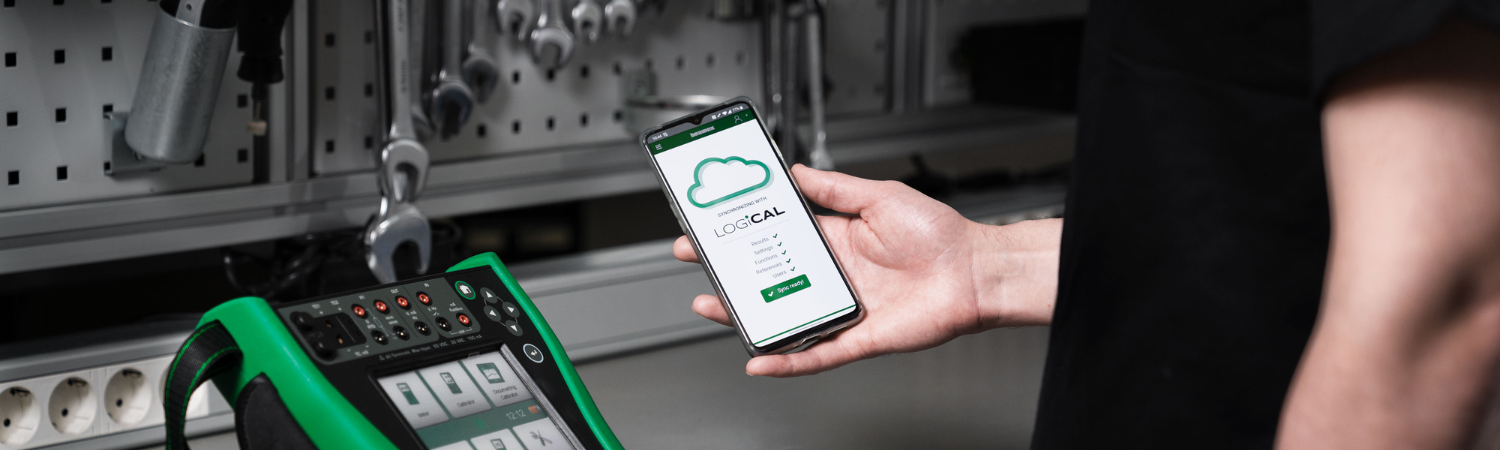
Aug 08, 2023
How Douglas Calibration Services reduces technicians’ workload and stress [Case Story]
Beamex LOGiCAL Calibration Management Software has helped Douglas Calibration Services improve ...
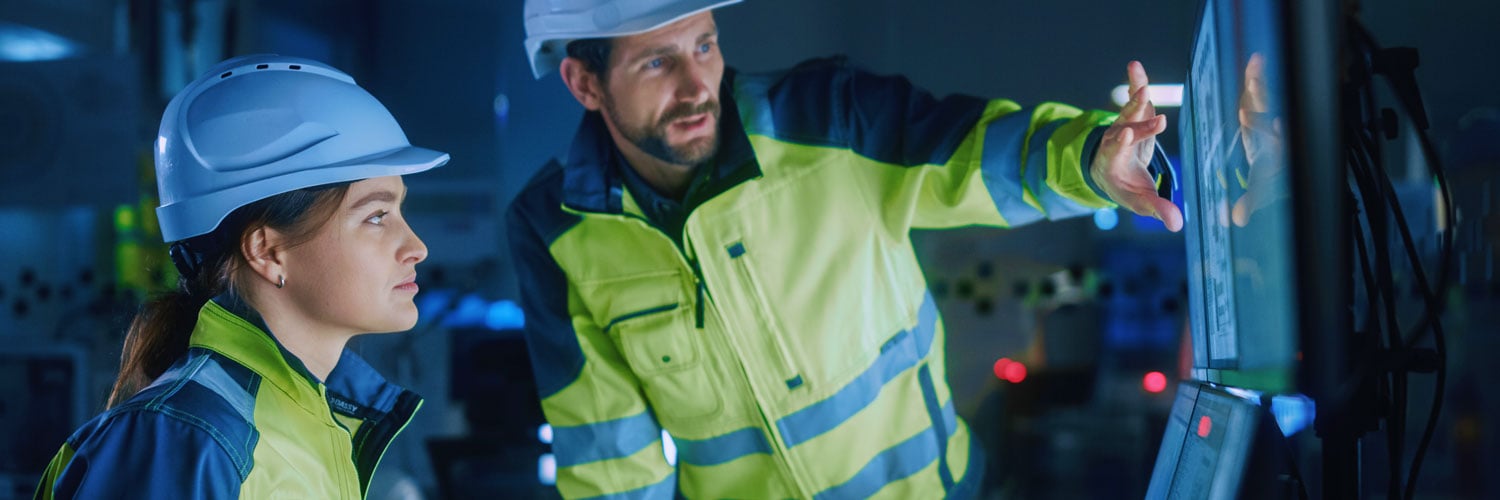
Apr 26, 2023
CMMS calibration module or dedicated calibration software?
When your computerized maintenance management system (CMMS) already has a calibration module, why ...
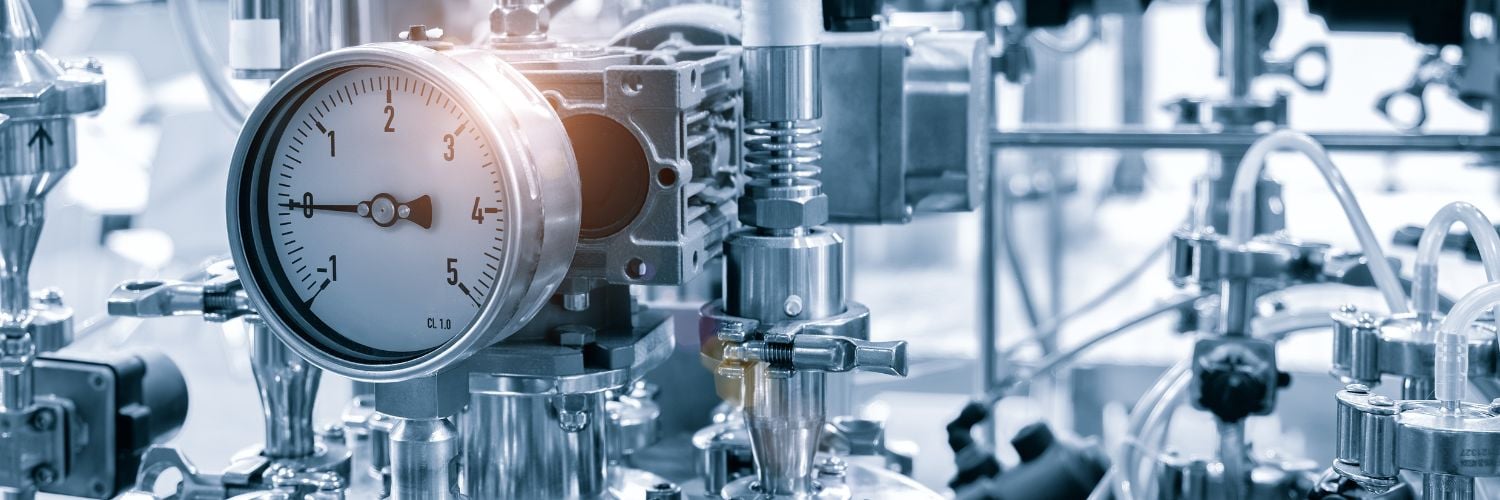
Sep 22, 2022
Ensuring sustainable management of process safety for chemicals
In the chemicals industry, safety is priority number one. But how do you ensure safety in a ...
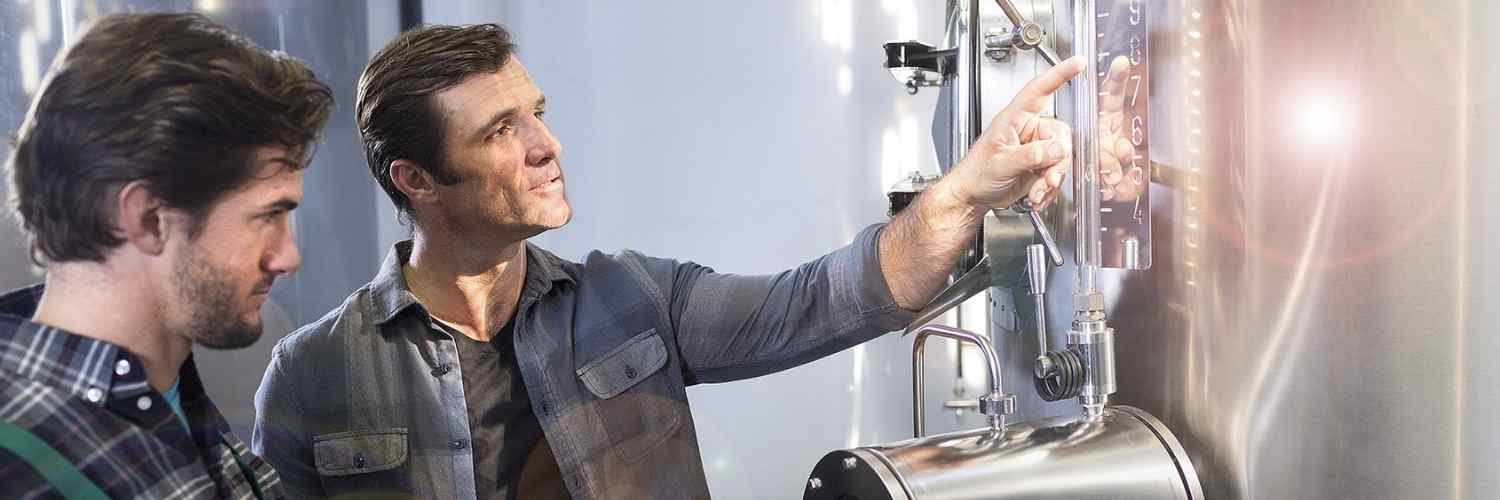
Jul 06, 2022
How automated calibration can help service companies be more competitive
Service companies that perform calibrations for the process industries operate in a challenging ...
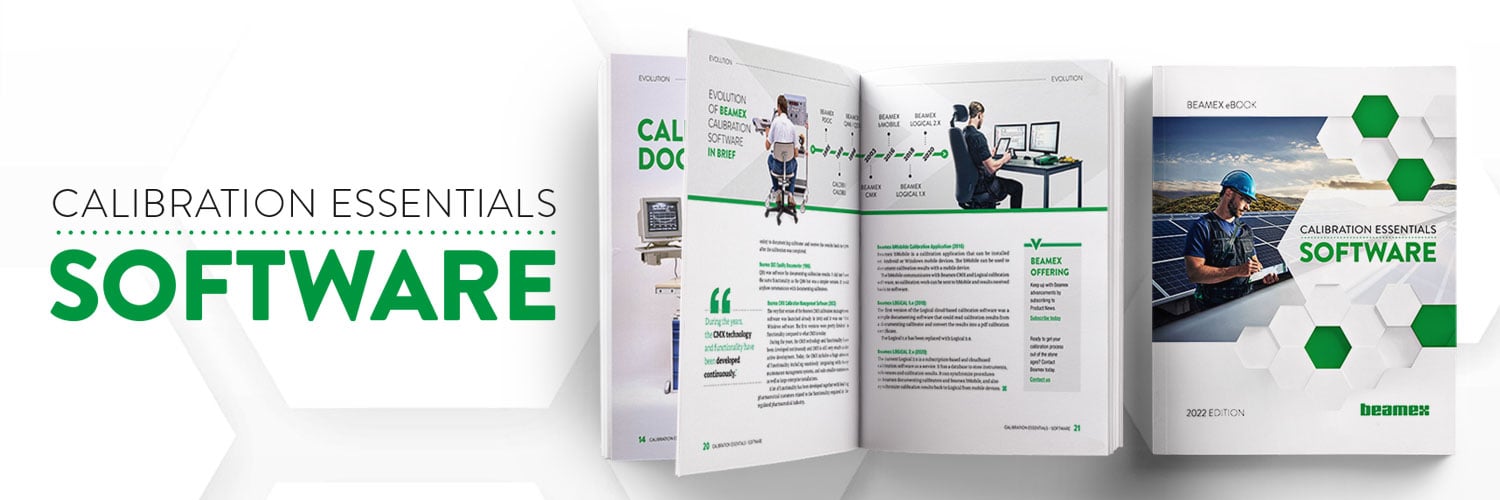
Apr 25, 2022
Calibration Management and Software [eBook].
In this blog post, we want to share with you an education eBook focusing on calibration management ...
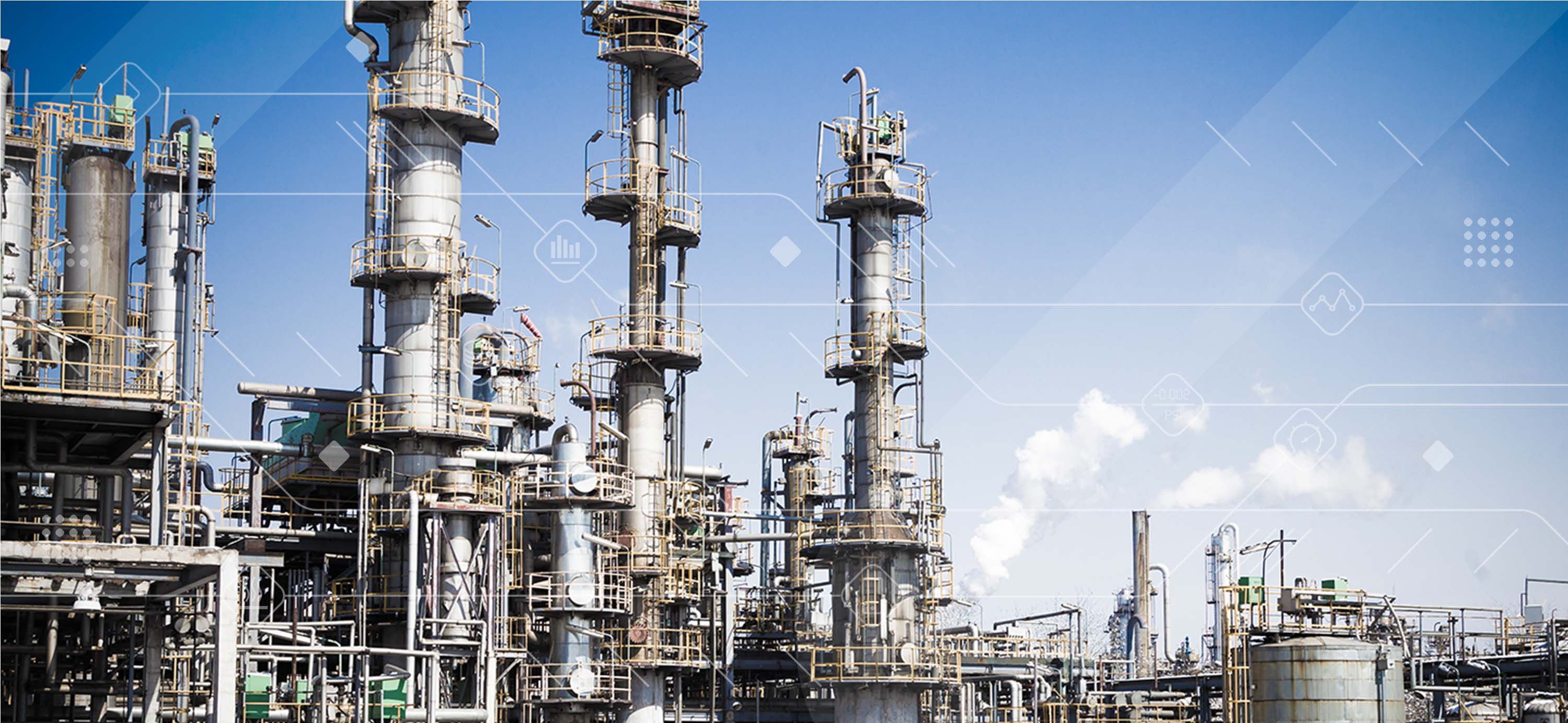
Feb 08, 2022
How to avoid safety and compliance issues in fine chemicals
Safety and compliance are non-negotiable in the fine chemicals industry, which produces complex, ...
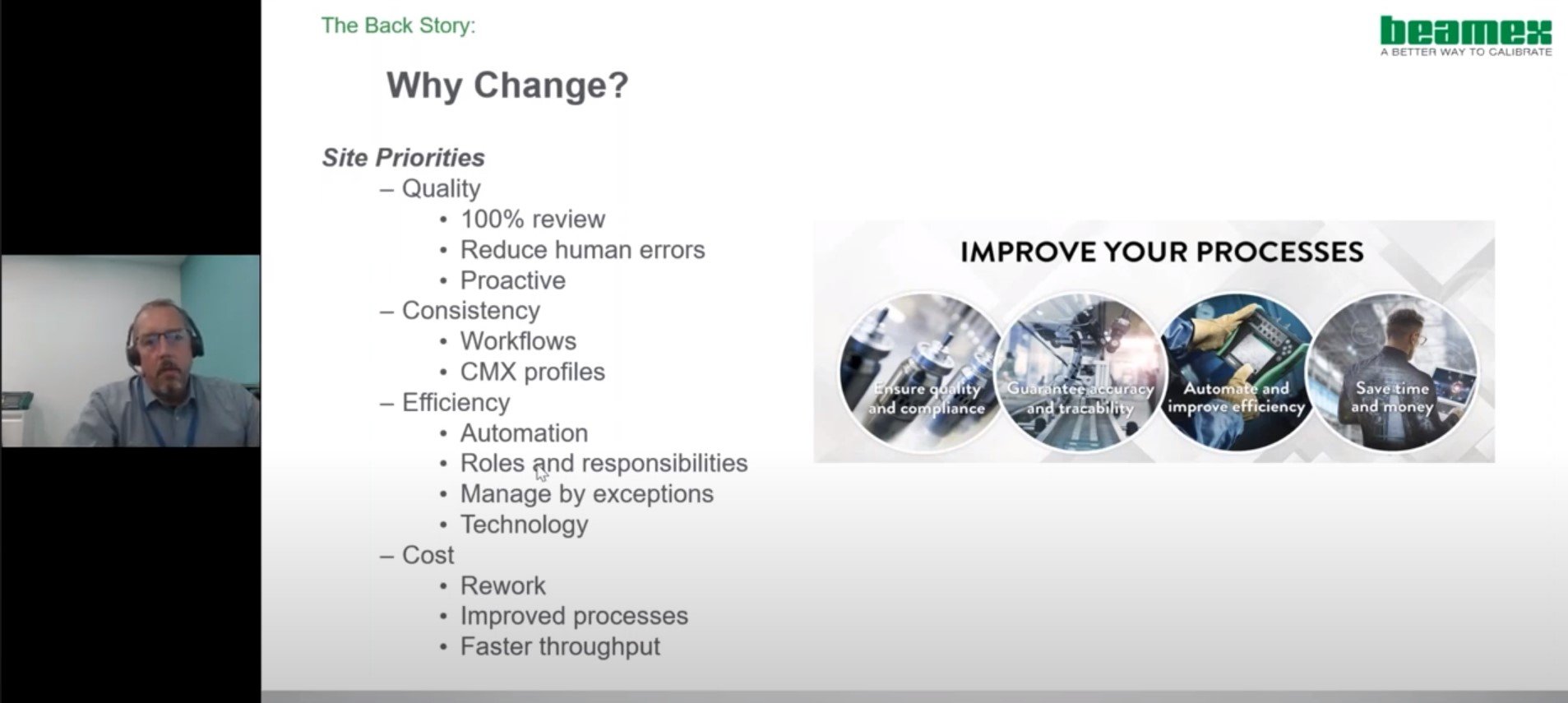
Jan 11, 2022
Calibration management - transition from paper-based to digital
A Tale of Three Steves Stephen Jerge, Calibration Supervisor for Lonza Biologics, a multinational ...
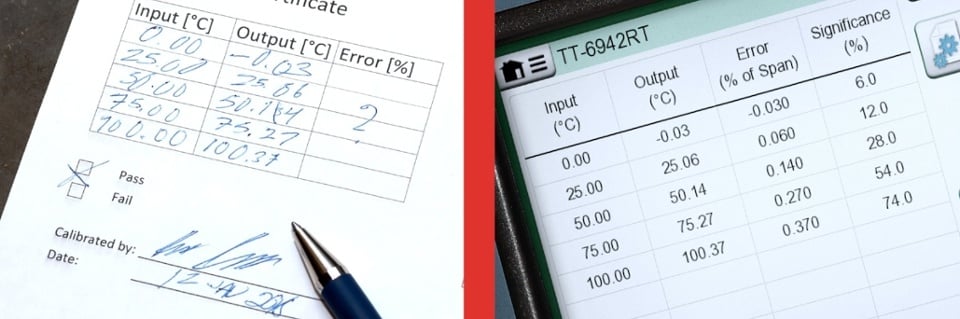
Mar 25, 2021
Manual Data Entry Errors
Many businesses still use a lot of manual entry in their industrial processes. This is despite the ...
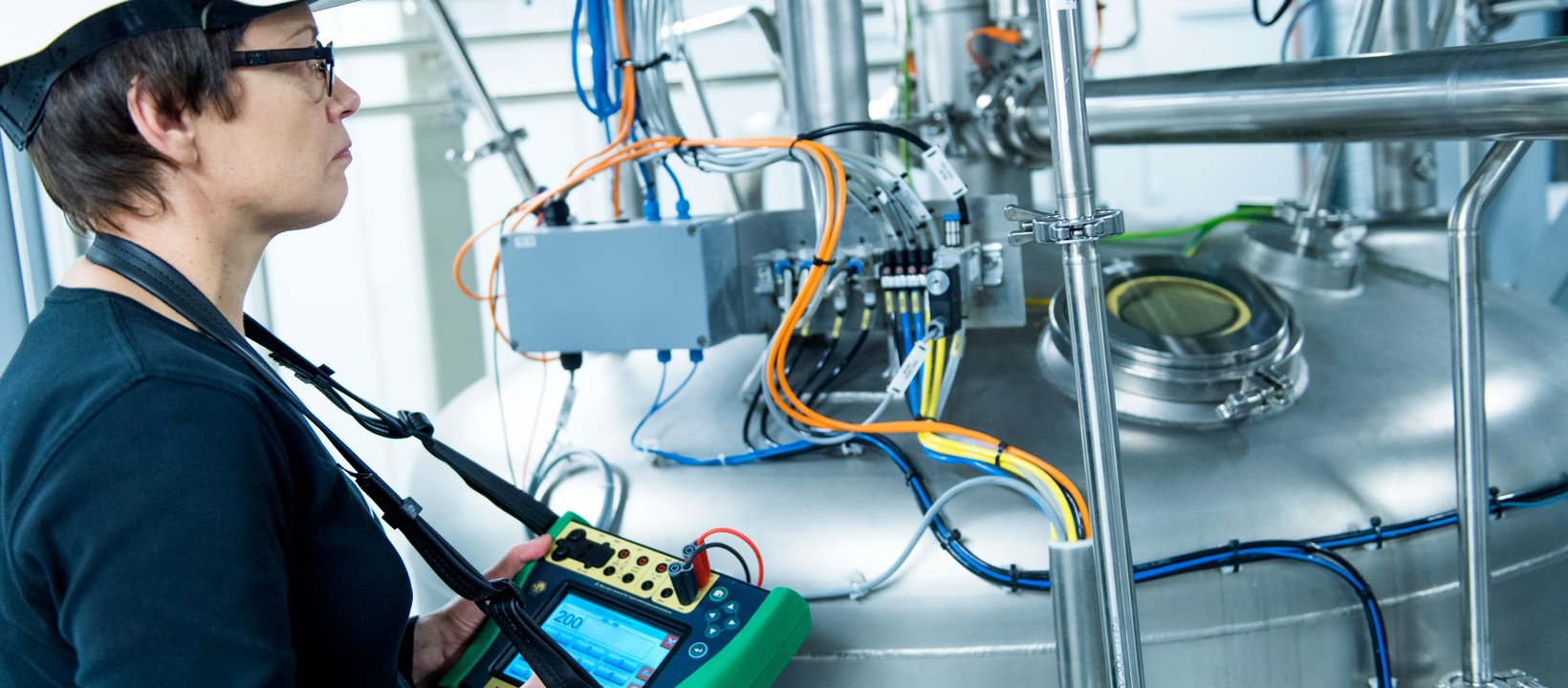
Apr 24, 2019
Optimal Calibration Parameters for Process Instrumentation
Many calibration technicians follow long-established procedures at their facility that have not ...
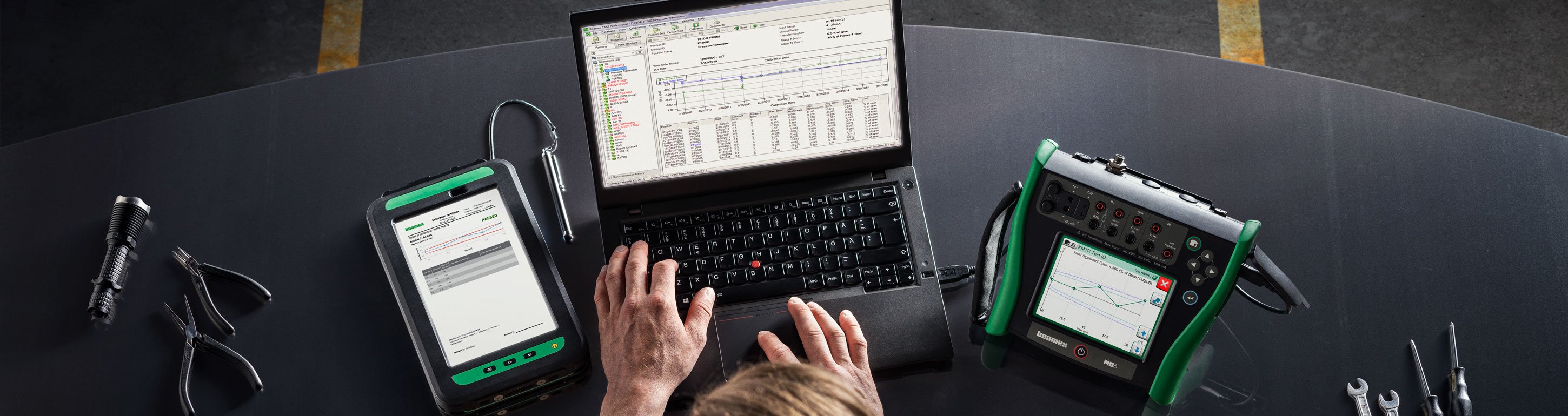
Nov 19, 2018
Do more with less and generate ROI with an Integrated Calibration Solution
Process instrument calibration is just one of the many maintenance related activities in a process ...